the difference between metal cutting and eDM

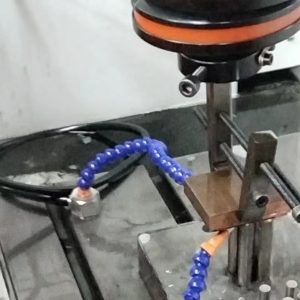
Metal cutting and electric discharge machining (EDM) are two common methods used in the manufacturing industry to shape and form metal materials. While both processes involve removing material from a workpiece, they differ in their approach and the results they produce. In this article, we will explore the basics of metal cutting and electric discharge machining, highlighting their differences and applications.
Metal cutting is a mechanical process that involves using a cutting tool to remove material from a workpiece. This can be done through various methods, such as turning, milling, drilling, or grinding. The cutting tool, typically made of a hard material like high-speed steel or carbide, is brought into contact with the workpiece, and the material is sheared or scraped away. This process is commonly used in industries like automotive, aerospace, and construction, where precision and accuracy are crucial.
On the other hand, electric discharge machining (EDM) and wire cut edm are non-traditional machining process that use electrical sparks to erode material from a workpiece. Unlike metal cutting, EDM does not involve physical contact between the tool and the workpiece. Instead, an electrode, usually made of copper or graphite, is used to generate a series of electrical discharges. These discharges create intense heat that melts and vaporizes the material, effectively removing it from the workpiece. EDM is often used for complex shapes and hard materials that are difficult to cut using conventional methods.
One of the key differences between metal cutting and EDM is the type of forces involved. In metal cutting, the cutting tool exerts a force on the workpiece, causing the material to deform and eventually separate. This force can be significant, especially when machining harder materials, and it requires a sturdy machine and tooling setup. In contrast, EDM relies on the thermal energy generated by the electrical discharges to remove material. As a result, there is no direct force applied to the workpiece, making it suitable for delicate or fragile materials.eg,many edm wire cut machine beginers often think about the force of friction which electrode wire can withstand, that’s unnessory.the copper electode or wire do not contact the workpiece,and the mirco gap electric discharges must be done to allow the edm operate nomally.
Another difference lies in the level of precision and surface finish that can be achieved. Metal cutting processes, especially those using computer numerical control (CNC) machines, can produce highly accurate and smooth surfaces. The cutting tool can be precisely controlled to remove material in small increments, resulting in tight tolerances and excellent surface finishes. EDM wire cut machine is known for its ability to machine intricate and complex shapes. However, the process may leave a rougher surface finish, requiring additional post-processing steps to achieve the desired smoothness.
In terms of applications, metal cutting is widely used in various industries for manufacturing components and parts. It is particularly suitable for mass production, where high volumes of identical parts need to be produced quickly and efficiently. EDM, on the other hand, is often employed in industries that require intricate and precise machining, such as aerospace, medical, and mold-making. It is commonly used to create complex shapes, deep cavities, or fine details that are difficult to achieve with traditional cutting methods.eg,the very small narrow slit machining,corner finish,the operators often add the circular arcs to the corners of workpiece drawings when the metal cutting is doing,that’s difficult the diameters of cutting tools must be less than diameter of circular arc.however,the electrode wire diameter of wire cut edm machine is from 0.05mm to 0.30mm that can meet most of requirements for the circular arcs of corners.
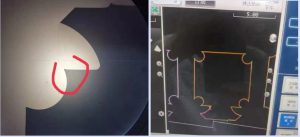
Metal cutting and electric discharge machining are two distinct processes used in the manufacturing industry. Metal cutting involves physically removing material from a workpiece using a cutting tool, while EDM uses electrical sparks to erode material. They differ in terms of forces involved, precision, surface finish, and applications. Understanding these differences can help manufacturers choose the most suitable method for their specific needs, ensuring efficient and accurate production.