molybdenum wire edm Benefits and efficiency.
molybdenum wire edm, or Electrical Discharge Machining, is a highly efficient and precise method of cutting and shaping metal parts. This technology uses a thin wire made of molybdenum to create electrical discharges that erode the material, resulting in intricate and accurate cuts. molybdenum wire edm is widely used in industries such as aerospace, automotive, and medical, where precision and quality are paramount.
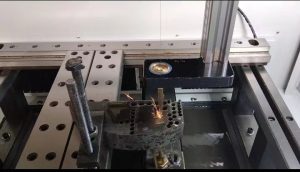
One of the key benefits of using molybdenum wire edm is its high level of precision. The thin wire allows for intricate cuts and shapes to be made with extreme accuracy, making it ideal for producing complex parts with tight tolerances. This precision is essential in industries where even the smallest deviation can lead to costly errors or failures.
The molybdenum wire edm is its ability to cut a wide range of materials, including hardened steels, exotic alloys, and conductive ceramics. This versatility makes it a valuable tool for manufacturers who work with a variety of materials and need a reliable method for cutting and shaping them.
In addition to its precision and versatility, molybdenum wire edm is also known for its efficiency. The process is non-contact, meaning there is no physical force applied to the workpiece, which reduces the risk of distortion or damage. This non-contact cutting also allows for faster cutting speeds and improved surface finishes, resulting in shorter production times and higher quality parts.
To further improve the efficiency of molybdenum wire edm, there are several key factors to consider. One important factor is the choice of wire material. Molybdenum wire is known for its high tensile strength and resistance to heat, making it ideal for EDM applications. However, there are different grades of molybdenum wire available, each with its own unique properties. Choosing the right grade of wire for the specific application can help optimize cutting performance and efficiency.
molybdenum wire edm is cutting a workpiece at high efficiency youtube video
Another factor to consider is the wire diameter. Thinner wires are typically used for finer cuts and tighter tolerances, while thicker wires are better suited for rougher cuts and faster cutting speeds. By selecting the appropriate wire diameter for the job, manufacturers can achieve the desired results with maximum efficiency.
Electrode wire material and diameter, other factors that can impact the efficiency of molybdenum wire edm include machine settings, flushing conditions, and cutting parameters. Properly setting up the machine, maintaining a consistent flushing system, and adjusting cutting parameters such as voltage, current, and wire speed can all contribute to improved cutting performance and efficiency.
Therefore, molybdenum wire edm offers a wide range of benefits for manufacturers looking to achieve precise, efficient, and high-quality cuts. By understanding the key factors that influence cutting performance and efficiency, manufacturers can optimize their processes and maximize the benefits of this advanced technology. With the right tools, materials, and techniques, molybdenum wire EDM can help manufacturers stay competitive in today’s fast-paced and demanding industries.